Solutions
Camron Consulting is focused on providing innovative solutions for a large and diverse base of regional, and local companies, including those operating in industries with unique supply chain requirements.
-
Supply Chain Management
Audit and analysis of functional business processes and procedures. Benchmark costs and performance against industry. Integrations planning and design. Implementation of measurement systems to drive improvements. Change facilitation. Project management. Camron takes all of these capabilities and roles them up into a “Value Proposition.”
- Dashboards
- Warehouse Design + Optimization
- Business Processes
-
Distribution & Logistics Strategy
Long-range plans to meet corporate objectives and establish competitive advantages. Our models are used for warehouse and plant location analysis and for inventory level determination. Modeling of facilities, materials flow and customer service policies.
- Network Models(JDA) I2
- Visual Communication
-
Transportation
Transportation cost-reduction strategies, carrier rate and accessorial charge negotiations (all models) improvement programs, consolidations, stop-offs, pooling, zone skipping, mode alternatives, and private carriage. Operational analysis. Development of policies and procedures and the preparation of related manuals and routing guides.
- Carrier Rates
- Develop RFPs
Dashboards
- Visual presentation of performance measures
- Ability to identify and correct negative trends
- Facility to measure efficiencies/inefficiencies
- Ability to generate detailed reports showing new trends
- Informed decisions based on collected business intelligence
- Capacity to align strategies and organizational goals
- Lower time requirement compared with running multiple reports
- Total, instant visibility of all systems
- Quick identification of data outliers and correlations
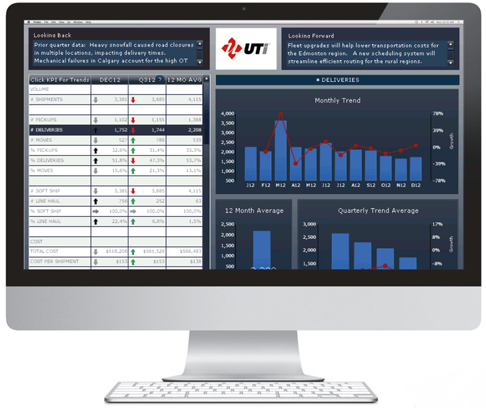
Dashboards allow managers to monitor the contribution of the various departments in their organization. To gauge exactly how well an organization is performing overall, digital dashboards allow you to capture and report specific data points from each department or KPI within the organization, thus providing a “snapshot” of performance.
Warehousing Design and Improvement
Improvements to layouts and operations to reduce space and labour requirements and to increase customer service performance levels. New facility design. CAD and simulation capabilities. Operations analysis, handling equipment specifications, and programs to reduce costs and increase throughout velocities. Evaluate the need for outsourcing and, if needed, select the best qualified third party logistics providers (3PLs).
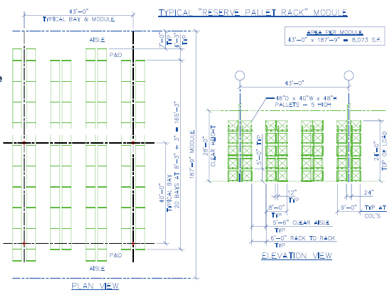
Business Process Re-engineering
Capabilities are used to identify the best plant/distribution locations and test the impact of service and/or inventory requirement changes on the network. By determining the best overall network our modeling capabilities extend to global networks as well as regional, area and local networks. A logistics network optimized to improve customer service and minimize operating cost is a fundamental requirement for the winning enterprise. Determination of the network is a process incorporating strategic and tactical elements. Our four-step approach provides our customer with a balanced approach to the art and science of network design.
- Define the business and client requirements creating a competitive advantage.
- Define and quantify the value of the competitive advantage.
- Create operational objectives in terms of the current capability and relative costs.
- Examine logistics operations, organization structure, key processes, enabling tools and technology, and key performance indicators.
- Collect, organize and analyze financial, historical production, inventory, shipment, and productivity data.
- Observe logistics operations from management and operator perspectives, including interviews with key personnel in each function.
- Assess interactions with external environments including customers, suppliers, manufacturing sites, maintenance contractors and other external suppliers.
- Interview the key business partners for impact of operations on external suppliers and customers.
- Prepare a SWOT analysis of the baseline conditions.
RELEVANT BENCHMARKING
- Analyze the current logistics baseline, identifying the relevant categories for benchmarking.
- Identify documented sources for leading practices in logistics and supply chain.
- Develop benchmarking questions to survey a relevant cross-section of industry respondents.
- Collect and catalogue the benchmarking data, identifying best practices for relevant categories.
- Prepare a side-by-side comparison between the current baseline and benchmarked best practices.
- Identify gaps between the current baseline and benchmarked best practices.
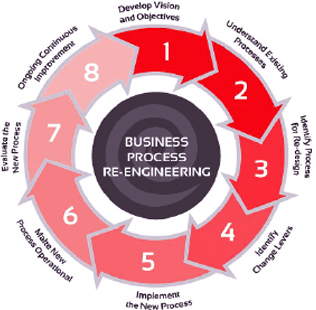
- Assess the risks and benefits associated with the status quo versus best practice.
- Identify key opportunities for improvement.
- Describe recommendations and tactics to close the gap for key opportunities.
- Develop the path-forward plan to achieve excellence in logistics.
Network Optimization
-
Data Collection and Organization
- Clearly define the elements of data to be collected.
- Collect, organize and analyze historical production, inventory and shipment data.
- Use assumptions, forecast and logistics strategy elements to transform the historical data to the best, worst and most likely picture of the future.
- Prepare the data to be used in the numerical network modeling.
-
Network Modeling
- Select the appropriate modeling tool.
- Model the current network to prove the accuracy of the data and model rules. This creates a baseline with which alternatives will be compared.
- Model alternatives and scenarios that support the scenario of the model. Make adjustments to each scenario to test sensitivity volume, cost and service drivers.
- Fine tune the alternatives providing the desired results until the optimum solution is reached.
- Define the benefits and risks associated with each alternative. Document the trade-offs between the alternatives.
-
Define the Recommended Network
- The strategic “fit” of the recommended network.
- The number and locations of distribution facilities.
- The products and inventories to be stored in each facility.
- The service levels and customers assigned to each facility.
- The capital required to build the network, the fixed and variable cost of ongoing network operations, and the financial benefits of the network.
- The path and resources required to transition from the current network to the recommended network.
Network Models
Capabilities are used to identify the best plant/distribution locations and test the impact of service and/or inventory requirement changes on the network. By determining the best overall network, our modeling capabilities extend to global networks as well as regional, area and local networks. A logistics network optimized to improve customer service and minimize operating cost is a fundamental requirement for the winning enterprise. Determination of the network is a process incorporating strategic and tactical elements. Our four-step approach provides our customer with a balanced approach to the art and science of network design.
- The business and customer requirements that create competitive differences are defined in terms of logistics support and functionality.
- The value of the competitive advantage is described and quantified.
- The logistics support and functionality are defined in terms of the current capability and relative costs.
- A conceptual description and model of the network strategy.
Visual Communications
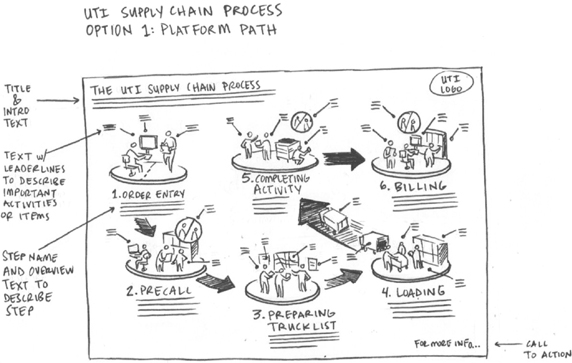

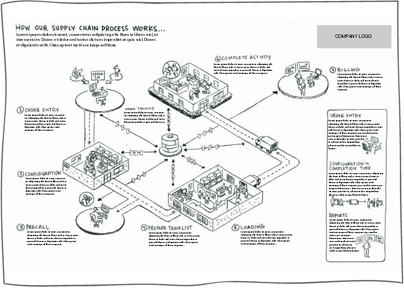
Here’s a result of how we can define and refine your processes…
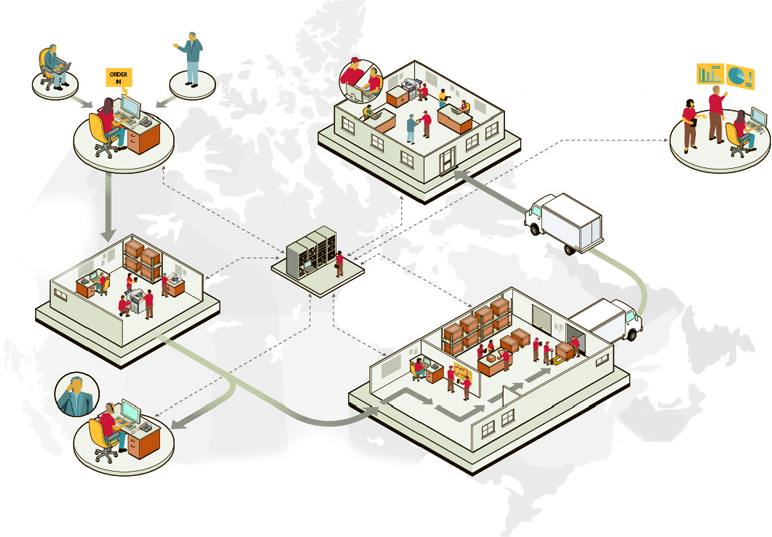
- Order Entry
All activity orders are entered in the system. Activities include pickups, deliveries and relocations. All data entry fields must be verified to the customer bill of lading prior to submitting the order to the system.
- Configuration
Product is removed from the warehouse inventory as per the pick ticket and staged for pre assembly if required. If product is pre-assembled it will be tested and packaged for delivery. The product is staged when completed in the appropriate bin location within the warehouse for pick up by the delivery crews.
- Precall
A precall is guaranteed on all orders in the system 48 hrs in advance but we can arrange as long as we have 1 full business day prior to the scheduled request. The issue is one of connectivity with the customer – it not always possible to get a hold the customer the first time and with phone tag it can take longer. The dispatcher will attempt to contact the customer at least twice before it is escalated to the owner of the order. If the precall is unsuccessful twice, an automated email will be sent to the owner providing the details. The owner must then provide alternate information or authorization to attempt without precall.
- Prepare Truck List
Each day, the dispatcher prepares the truck list prior to the clients cut off time. All information is verified with the paperwork to ensure accurate information. The dispatcher ensures all orders are assigned to the correct route to guarantee to best geographical coverage. The truck lists are sent to the customer to confirm the information is correct to prepare for scheduling. All paperwork is attached to the truck lists for the drivers.
- Loading
Delivery crews arrive to the warehouse location to pick up the goods that are to be delivered. Goods are removed from the bin locations for the appropriate run utilising the manifest or tablet. The product is confirmed with the paperwork provided for accuracy of piece count and product that is to be delivered. Activity is prioritised in order with ETA provided. Truck is loaded in the appropriate manner depending on the goods
being moved as set in the load procedure process. Delivery crew departs the warehouse. - Complete Activity
Delivery crew arrive to the customers location within the ETA provided. The goods are delivered to the final location as indicated by the customer. If required all packing materials are removed from
customer’s location. Drivers obtain signature on paperwork or tablet. The completion of the activity is communicated to dispatch within 15 minutes electronically or by phone. - Billing and Reports
All orders are to be closed and billed by the dispatcher within 72 hours of completion. All orders are billed based on the customer SOP and quotes which have been pre-approved by the customer. The client can log onto the system and view the billing details once entered by the dispatcher and all available reports & KPI’s based on past activity.
Transportation
Transportation cost-reduction strategies, carrier rate and accessorial charge negotiations (all models) improvement programs, consolidations, stop-offs, pooling, zone skipping, mode alternatives, and private carriage. Operational analysis. Development of policies and procedures and the preparation of related manuals and routing guides.
- Carrier Rates
- Develop RFPs
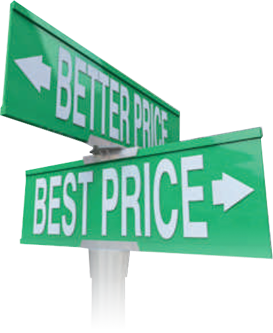
Carrier Rate Negotiation Methodology
The key to a successful supply chain is planning not only how to distribute your product, but also how to bring it back — both customer returns and obsolete products. Managing returns effectively allows you to recapture value or reduce write-offs, while keeping your customers happy. Camron will help you design, plan and implement a reverse supply chain that supports your profit goals and provides you the maximum value for your assets. We bring to reverse logistics the exacting management, resources and technology required to increase control and asset recovery, improve information management and save administrative time.